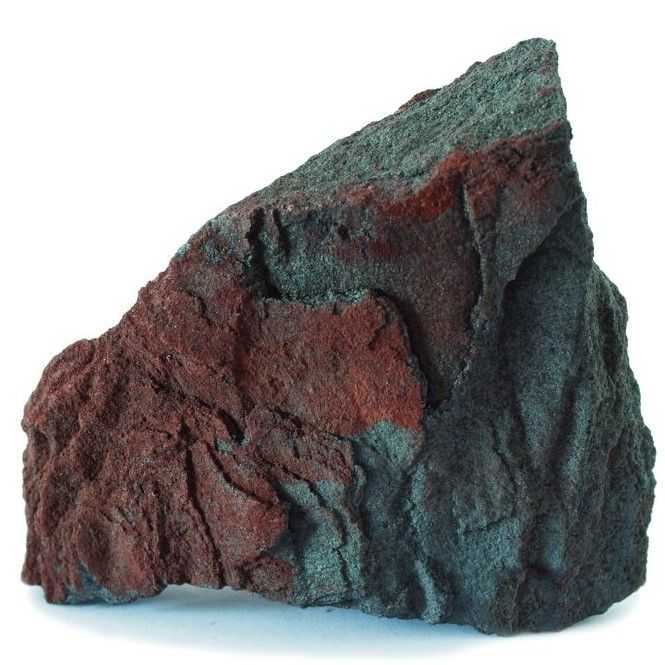
- Iron is a metal that is the fourth most abundant element in the earth’s crust. In other words; The earth’s crust contains 5% iron ore. Iron does not exist in pure form in nature and is found in the form of mineral ore. The most common iron compounds in nature; They are in the form of ferrous iron (bivalent) and ferric iron (trivalent). According to the location of iron mines, iron ore also has various compositions. Rocks that contain more than 20% iron are known as iron ore.
- There are more than 300 types of minerals that contain the element iron. In the meantime; 5 iron ores are known as the most important iron ores. These 5 minerals are: 1- Magnetite 2- Hematite 3- Goethite 4- Sedrite 5- Pyrite.
- Among these 5 minerals; Hematite and magnetite rocks have the highest percentage of iron. Hematite iron ore is type 3 iron oxide and its chemical formula is Fe2O3. This mineral has 70% iron and is red in nature. The observed color after iron corrosion is due to the formation of this type of oxide.
Types of iron ore
- In terms of structure, it is divided into 4 categories:
- Sedimentary mines
- Mines of sulfur origin
- Volcanic and hydrothermal sources
- Mines resulting from the removal of impurities from the rocks
- According to the location of the mines; The compositions of iron ores are different from each other. Considering these differences; There are more than 300 types of iron ore. Rocks with less than 20% iron in their composition are not known as iron ore. Some stones with high iron grade are:
Hematite stone
- Hematite stone is type 3 iron oxide and its chemical formula is Fe2O3. This mineral has 70% iron and is red in nature. The observed color after iron corrosion is due to the formation of this type of oxide. You can see an example of it below.
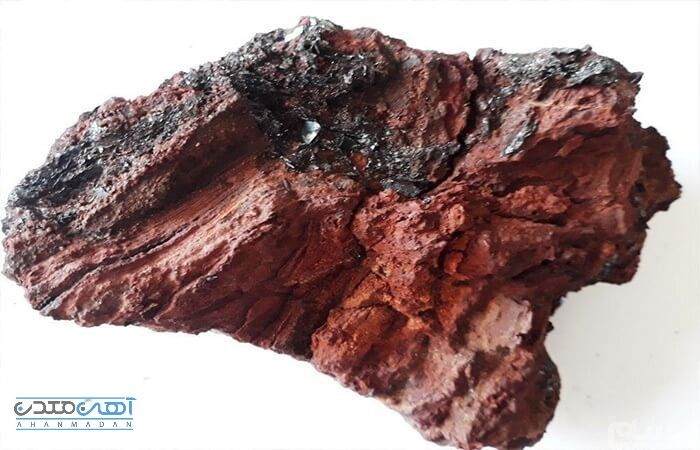
Magnetic stone
- Magnetite is a type of this product that consists of a combination of type two iron oxide and type three iron oxide, and its chemical formula is Fe3O4. Magnetite iron ore is seen in black and has 72.4% iron. Of course, divalent iron oxide (FeO) is very rare in nature and exists as a compound in magnetite mineral.
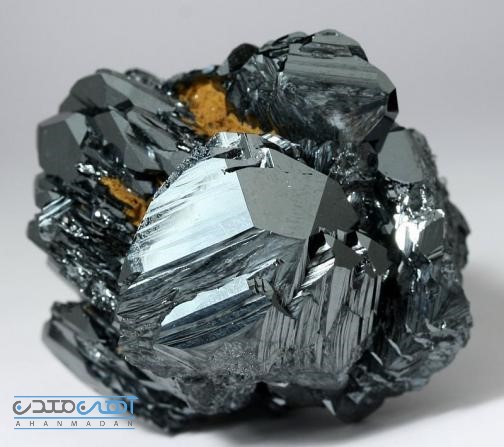
Siderite stone
- The chemical formula of siderite stone is FeCO3 and there is 48.2% iron in its composition. Although it is not as rich in iron as magnetite and hematite, it is one of the good stones.
- The processing steps of this magnetite product are easier than hematite. It also has a lower processing cost than hematite processing. For this reason, magnetite is more in demand in Iran’s domestic markets. In Iran, there are more reserves of magnetite, so there is not much investment for hematite processing. The grade of iron in hematite is lower than that of magnetite, and a lot of money must be spent to increase its purity. The low grade of hematite causes a lot of waste to be produced, as a result, the production efficiency is reduced.
- Despite all these, the demand of the industry is increasing tremendously. Steel factories are the main consumers of iron ore; Almost 98% of iron ore harvested from mines is used in steel factories. These increasing needs have caused hematite reserves to be taken into consideration. In some countries that are facing a shortage of iron resources, they even use siderite.
Different forms of iron ore
- According to the needs of industries and uses, iron ore is prepared in various forms. This stone exists in the form of pellets, granules, concentrates and sponge iron.
Concentrate
- A method for processing magnetite iron ore; Production of iron ore concentrate. To obtain iron ore, one must first identify mines that have a high percentage of iron. This work is done by mining engineers and specialists in this field. The extracted ore is first crushed and then ground. In the next step, it is sieved and also washed. By flotation method or by using magnetic separators, the grade of iron is increased. In the next step, disturbing elements such as sulfur and phosphorus, which cause the quality of the concentrate to go down; are deleted. The last step is dewatering from concentrate and wastewater treatment. The resulting concentrate is in the form of black powder and it is used to make iron pellets and sponge iron.
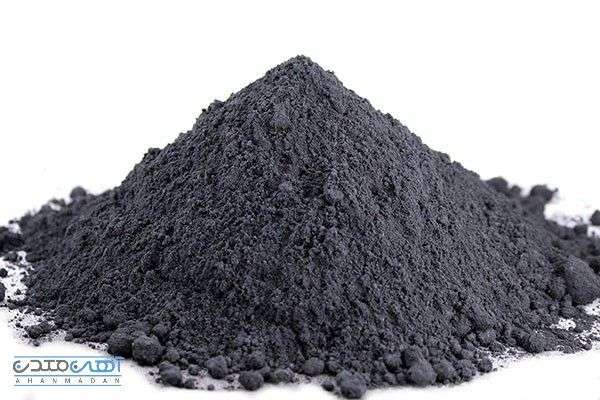
Stone granulation
- The second method for iron ore processing is granulated ore production. The dry method is used to produce this type of product. Then with the help of magnetic methods; High purity iron is separated from waste materials and low purity iron. This type of stone exists in two types of fine grain and coarse grain. Granulated stones are used only in blast furnaces and are not applicable in the direct method; Because its purity is low. Because the ability to regenerate granular minerals is low; The consumption of this type of stone has decreased.
Pellet
- Iron concentrate powder is mixed with some materials such as water, bentonite, cement, lime, organic materials and milk of lime. The resulting mixture enters the pellet machine and finally raw iron pellets are produced. in order to dry and harden the pellet; It is in an oxidizing atmosphere; They heat up to the necessary temperature to soften the stone. At this stage, care should be taken that the degree of porosity of the pellet does not decrease and also that it does not crack during cooling. The ball is spherical and porous. Pellets are mostly used in blast furnaces and sponge iron production.
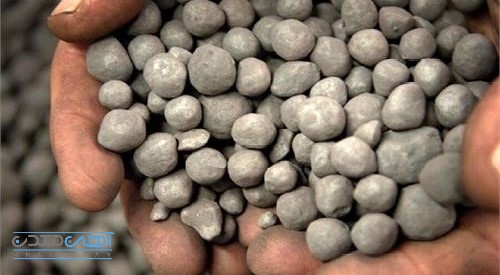
Sponge iron
This type of iron is the product of the direct reduction method. In the direct method, without the need to melt the iron ore, it is heated and its oxygen can be removed during the oxidation and reduction process. The produced product is porous, that is why it is called sponge iron. To make this type of iron, pellets with a purity of 67% are used. In this method, coal (elemental carbon) or natural gas (reducing gas) is used as a regenerating agent. The produced sponge iron has a grade of about 84%, which is higher than the pellet grade.
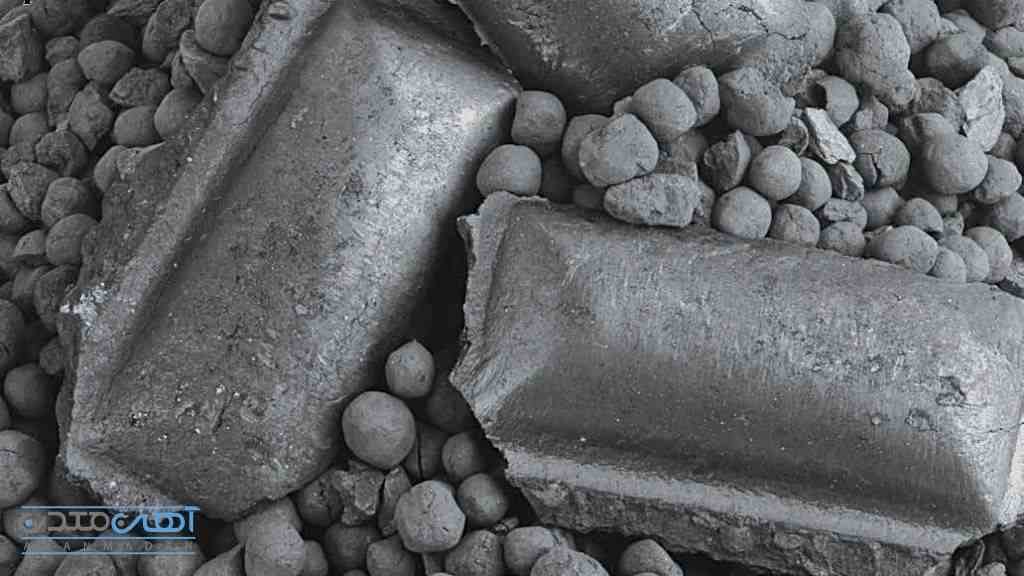
Uses of iron ore
- This product is widely used in concrete, cement and drilling mud industries as a heavy intermediate. It is also used in the coal industry. Due to its red color, hematite mineral is widely used as a pigment in various industries such as dyeing and stainless steel production. The main use of iron ore is in the production of iron alloys. Iron ore is used in two traditional and direct ways. traditional method; It is used to produce iron and steel in blast furnaces, but the direct method is used to recover pure iron.
Steel
- elemental iron; It is very unstable and quickly reacts with oxygen and produces iron oxide and so-called rust. In addition to being unstable, iron does not have high strength. To solve these disadvantages, resistant alloys are produced by combining iron with other materials, including various metals. Steel is the most important iron alloy and almost all the iron ore mined is used in steel industries. Because it is the main ingredient of different types of steel. Steel is an alloy of iron and carbon (carbon steel) that is used in many important industries. Among these industries that consume the most steel; We can mention the automotive industry, construction and architecture. Other industries such as bridge construction, dam construction, light and heavy machinery, railways, household appliances, shipbuilding, defense industries, etc. consume iron.
- blast furnaces used for steel production; They have a lot of pollution. An electric arc furnace is used to solve this problem. Graphite electrode is the most important component of the electric arc furnace and plays a fundamental and important role in steel and metallurgy industries. This type of electrode is a consumer electrode type; This means that it must be replaced after a while.