نام | نوع | واحد | محل بارگیری | قیمت | تغییرات | ||
---|---|---|---|---|---|---|---|
سنگ آهن دانه بندی توسعه فرآوری صنایع و معادن ماهان سیرجان | سنگ آهن دانه بندی | تن | کارخانه | 2,600,000 تومان |
ثابت
|
خرید | |
کنسانتره سنگ آهن توسعه معدنی و صنعتی صبانور | کنسانتره سنگ آهن | تن | کارخانه | 5,416,000 تومان |
ثابت
|
خرید | |
کنسانتره سنگ آهن گوهر زمین | کنسانتره سنگ آهن | تن | کارخانه | 5,561,000 تومان |
ثابت
|
خرید | |
کنسانتره سنگ آهن چادر ملو | کنسانتره سنگ آهن | تن | کارخانه | 4,200,000 تومان |
ثابت
|
خرید | |
کنسانتره سنگ آهن گلگهر | کنسانتره سنگ آهن | تن | کارخانه | 5,738,000 تومان |
ثابت
|
خرید | |
کنسانتره سنگ آهن سپاهان | کنسانتره سنگ آهن | تن | کارخانه | 5,313,000 تومان |
3%-
186,000تومان
|
خرید | |
کنسانتره سنگ آهن بین المللی اسم ایران | کنسانتره سنگ آهن | تن | کارخانه | 4,004,000 تومان |
ثابت
|
خرید | |
کنسانتره سنگ آهن کیهان صنعت کاسپین | کنسانتره سنگ آهن | تن | کارخانه | 5,061,000 تومان |
1.5%-
61,000تومان
|
خرید |
آهن فلزی است که از نظر فراوانی، چهارمین عنصر موجود در پوسته زمین است. به عبارتی؛ پوسته زمین حاوی 5% سنگ آهن است. آهن به صورت خالص در طبیعت وجود ندارد و به صورت کانی معدنی یا همان سنگ معدنی یافت میشود. رایجترین ترکیبات آهن در طبیعت؛ به صورت آهن فرو (دو ظرفیتی) و آهن فریک (سه ظرفیتی) هستند. با توجه به موقعیت معادن آهن، سنگ آهن نیز ترکیبات گوناگونی دارد. سنگهایی به عنوان سنگ آهن شناخته میشوند که در ترکیبشان بیش از 20% آهن وجود داشته باشد.
بیش از 300 نوع کانی وجود دارد که حاوی عنصر آهن است. در این میان؛ 5 کانی آهن به عنوان مهمترین سنگهای آهن شناخته میشوند. این 5 کانی عبارتند از: 1- مگنتیت 2- هماتیت 3- گوتیت 4- سدریت 5- پیریت.
از بین این 5 کانی؛ سنگهای هماتیت و مگنتیت بالاترین درصد آهن را دارند. سنگ آهن هماتیت، اکسید آهن نوع سه است و فرمول شیمیایی آن Fe2O3 میباشد. این کانی70% آهن دارد و به رنگ قرمز در طبیعت وجود دارد. رنگ مشاهده شده بعد از خوردگی آهن به دلیل تشکیل این نوع اکسید است.
انواع سنگ آهن
از نظر ساختار به 4 دسته تقسیمبندی میشود:
- معادن رسوبی
- معادن با منشاء سولفوری
- منابع با منشاء آتشفشانی و هیدروترمال
- معادن حاصل از خروج ناخالصی از درون سنگ ها
با توجه به موقعیت معادن؛ ترکیبات سنگهای معدنی آهن با یکدیگر متفاوت است. با توجه به این تفاوتها؛ بیش از 300 نوع سنگ آهن وجود دارد. سنگهایی که کمتر از 20% آهن در ترکیبشان وجود داشته باشد به عنوان سنگ آهن شناخته نمیشوند. برخی از سنگهای با عیار بالای آهن عبارتند از:
سنگ هماتیت
سنگ هماتیت، اکسید آهن نوع سه است و فرمول شیمیایی آن Fe2O3 میباشد. این کانی70% آهن دارد و به رنگ قرمز در طبیعت وجود دارد. رنگ مشاهده شده بعد از خوردگی آهن به دلیل تشکیل این نوع اکسید است. که در زیر نمونه آن را مشاهده میکنید.
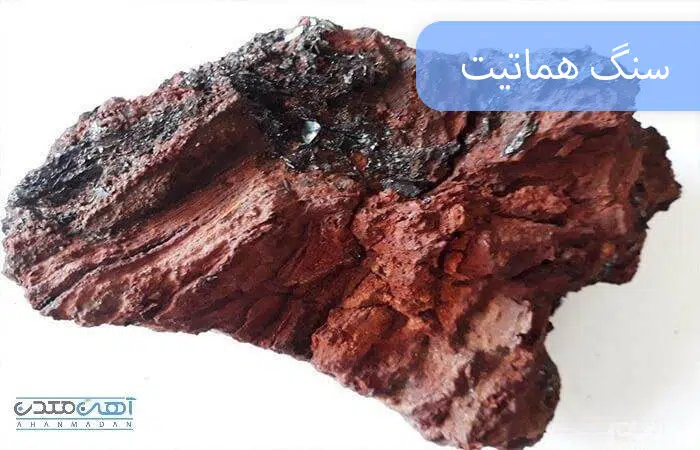
سنگ مگنتیک
مگنتیت نوعی از این محصول است که از ترکیب اکسید آهن نوع دو و اکسید آهن نوع سه تشکیل شده است و فرمول شیمیایی آن به صورت Fe3O4 میباشد. سنگ آهن مگنتیت به رنگ سیاه دیده میشود و 4/72% آهن دارد. البته اکسید آهن دو ظرفیتی (FeO) در طبیعت بسیار کمیاب است و به صورت ترکیب در کانی مگنتیت وجود دارد.
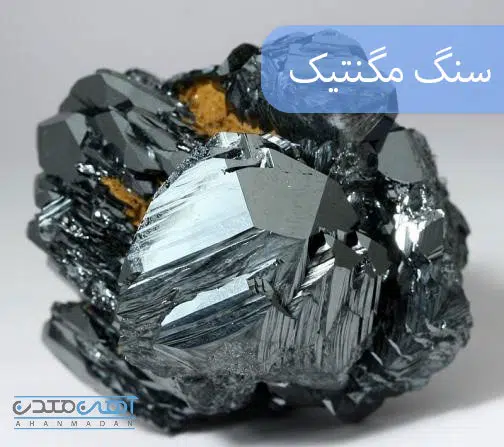
سنگ سیدریت
فرمول شیمیایی سنگ سیدریت FeCO3 است و 2/48% آهن در ترکیب آن وجود دارد. هرچند به اندازه مگنتیت و هماتیت غنی از آهن نیست ولی از دسته سنگهای خوب به شمار میآید. مراحل فرآوری این محصول مگنتیت نسبت به هماتیت آسانتر است. همچنین هزینه فرآوری کمتری نسبت به فرآوری هماتیت دارد. به همین دلیل در بازارهای داخلی ایران مگنتیت بیشتر مورد تقاضا است. در ایران ذخایر مگنتیت بیشتر است بنابراین برای فرآوری هماتیت خیلی سرمایه گذاری نشده است. عیار آهن در هماتیت پایینتر از مگنتیت است و برای بالا بردن خلوص آن باید هزینه زیادی صرف شود. پایین بودن عیار هماتیت موجب میشود باطله زیادی تولید شود، در نتیجه راندمان تولید پایین میآید. با وجود تمام این موارد، تقاضای صنعت به شدت در حال افزایش است. کارخانههای فولادسازی عمده ترین مصرف کننده سنگ آهن هستند؛ تقریبا 98% از سنگ آهن برداشت شده از معادن در کارخانههای فولاد به مصرف میرسند. این نیازهای روز افزون موجب شده تا ذخایر هماتیت نیز مورد توجه قرار گیرند. در برخی از کشورها که با کمبود منابع آهن روبرو هستند، حتی از سیدریت نیز استفاده میکنند.
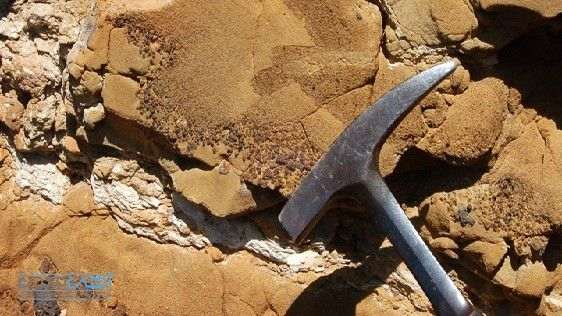

شکل های مختلف سنگ آهن
با توجه به نیاز صنایع و موارد مصرف، سنگ آهن به شکلهای گوناگونی تهیه میشود. این سنگ به شکل گندله, دانه بندی، کنسانتره و آهن اسفنجی وجود دارد.
کنسانتره
یک روش برای فرآوری سنگ آهن مگنتیت؛ تولید کنسانتره سنگ آهن است. برای به دست آوردن سنگ آهن، ابتدا باید معادنی که درصد بالایی آهن دارند را شناسایی کرد. این کار توسط مهندسان معدن و متخصصان این رشته انجام میشود. سنگ معدن استخراج شده ابتدا خرد شده و سپس آسیاب میشود. در مرحله بعد الک میشود و همچنین عملیات شستشو روی آن انجام میگیرد. با روش فلوتاسیون و یا با استفاده از جداکنندههای مغناطیسی عیار آهن افزایش مییابد. در مرحله بعد عناصر مزاحم مانند گوگرد و فسفر که موجب میشوند کیفیت کنسانتره پایین بیاید؛ حذف میشوند. آخرین مرحله آبگیری از کنسانتره و عملیات تصفیه پساب است. کنسانتره حاصل به شکل پودر سیاه رنگ است و از آن برای ساخت گندله آهن و آهن اسفنجی استفاده میشود.
سنگ دانه بندی
دومین روش برای فرآوری سنگ آهن، تولید سنگ دانهبندی شده است. برای تولید این نوع محصول از روش خشک استفاده میشود. سپس با کمک روشهای مغناطیسی؛ آهن با خلوص بالا را از مواد زائد و آهن با خلوص پایین جدا میکنند. این نوع سنگ در دو نوع دانه ریز و دانه درشت وجود دارد. از سنگهای دانهبندی شده فقط در کورههای بلند استفاده میشود و در روش مستقیم کاربردی ندارند؛ زیرا خلوص آن پایین است. به دلیل اینکه قابلیت احیا پذیری کانیهای دانه بندی شده کم است؛ مصرف این نوع سنگ کاهش یافته است.
گندله
پودر کنسانتره آهن با برخی مواد از قبیل آب، بنتونیت، سیمان، آهک، مواد آلی و شیر آهک مخلوط میشود. ترکیب حاصل وارد دستگاه گندله ساز شده و در نهایت گندله آهن خام تولید میشود. به منظور خشک شدن و سخت شدن گندله؛ آن را در اتمسفر اکسنده؛ تا دمای لازم برای نرم شدن سنگ حرارت میدهند. در این مرحله باید دقت شود که درجه تخلخل گندله پایین نیاید و همچنین در هنگام سرد شدن نیز ترک نخورد. گندله به شکل کروی و متخلخل است. از گندله بیشتر در کورههای بلند و نیز تولید آهن اسفنجی استفاده زیادی میشود.
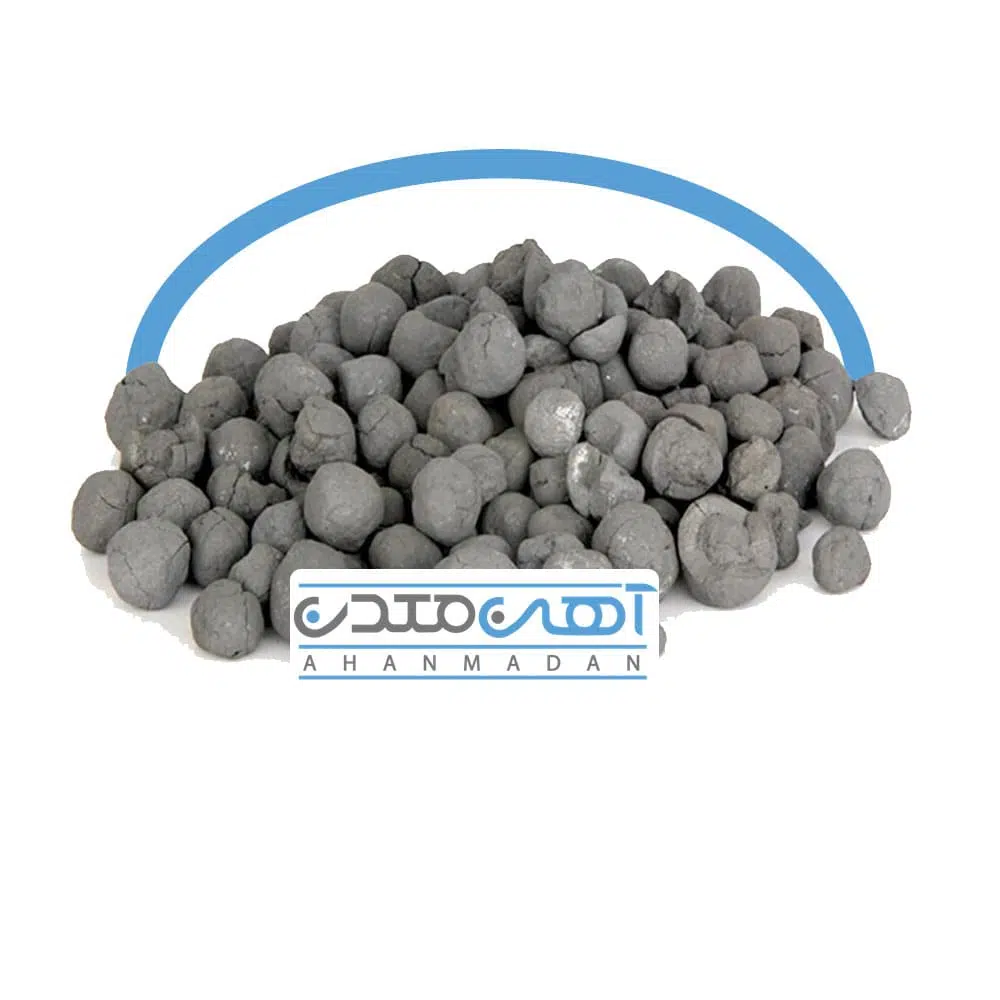
آهن اسفنجی
این نوع آهن محصول روش احیای مستقیم است. در روش مستقیم، بدون اینکه نیازی به ذوب سنگ آهن باشد آن را حرارت داده و طی فرایند اکسایش و کاهش میتوان اکسیژن آن را حذف کرد. محصول تولید شده متخلخل است به همین دلیل آهن اسفنجی نام دارد. برای ساخت این نوع آهن از گندله با خلوص 67% استفاده میشود. در این روش از زغال سنگ (کربن عنصری) و یا گاز طبیعی (گاز کاهنده) به عنوان ماده احیا کننده استفاده میشود. آهن اسفنجی تولید شده عیاری حدود 84% دارد که از عیار گندله بیشتر است.
موارد مصرف سنگ آهن
از این محصول در صنایع بتن، سیمان و گل حفاری به عنوان واسطه سنگین استفاده زیادی میشود. همچنین در صنعت زغال سنگ نیز کاربرد دارد. از کانی هماتیت به علت دارا بودن رنگ قرمز، در صنایع مختلفی از قبیل رنگسازی و تولید ضد زنگ به عنوان رنگدانه استفاده فراوانی میشود. عمدهترین مصارف کانی آهن در تولید آلیاژهای آهن است. سنگ معدن آهن به دو روش سنتی و مستقیم مورد استفاده قرار میگیرد. روش سنتی؛ برای تولید آهن و فولاد در کورههای بلند کاربرد دارد اما روش مستقیم برای احیای آهن خالص استفاده میشود.
فولاد
آهن به صورت عنصر؛ بسیار ناپایدار است و به سرعت با اکسیژن واکنش داده و اکسید آهن تولید میکند و به اصطلاح زنگ میزند. آهن علاوه بر ناپایدار بودن، از استحکام بالایی نیز برخوردار نیست. برای رفع این معایب از ترکیب آهن با سایر مواد از جمله انواع فلزات، آلیاژهای مقاوم تولید میشود. فولاد مهمترین آلیاژ آهن است و تقریبا تمامی سنگ آهن استخراج شده در صنایع فولادی مصرف میشود. زیرا ماده اصلی تشکیل دهنده انواع مختلف فولاد است. فولاد نوعی آلیاژ آهن با کربن است (فولاد کربنی) که در بسیاری از صنایع مهم کاربرد دارد. از جمله این صنایع که بیشترین مصرف فولاد را دارند؛ میتوان به صنعت خودروسازی، ساخت و ساز و معماری اشاره کرد. صنایع دیگری مانند پلسازی، سدسازی، ماشیتآلات سبک و سنگین، راه آهن، لوازم خانگی، کشتیسازی، صنایع دفاعی و … مصرف کننده آهن هستند.
کورههای بلند که به منظور تولید فولاد استفاده میشوند؛ آلودگی زیادی دارند. برای رفع این معضل از کوره قوس الکتریکی استفاده می شود. الکترود گرافیتی مهمترین جزء کوره قوس الکتریکی است و در صنایع فولاد و متالورژی نقش اساسی و مهمی دارد. این نوع الکترود از نوع الکترود مصرفی می باشد؛ به این معنی که بعد از مدتی باید تعویض شود.
جمع بندی
آهن بهصورت خالص در طبیعت وجود ندارد و بهصورت کانی معدنی یا همان سنگ معدن یافت میشود. رایجترین ترکیبات آهن در طبیعت؛ در قالب آهن فرو(دو ظرفیتی) و آهن فریک( سه ظرفیتی) هستند. با توجه به موقعیت معادن آهن سنگ آهن نیز ترکیبات گوناگونی دارد. سنگهایی بهعنوان سنگ آهن شناخته میشوند که در ترکیبشان بیش از ۲۰٪ آهن وجود داشته باشد. سنگهای کاربردهای گوناگونی وجود دارد که میتوان به کارکرد آن در صنایع بتن، سیمان و زغال سنگ اشاره کرد.