سنگ آهن کلوخه
نام | نوع | واحد | محل بارگیری | نوع پرداخت | قیمت | تغییرات | ||
---|---|---|---|---|---|---|---|---|
سنگ آهن کلوخه صبانور | سنگ آهن کلوخه | تن | کارخانه | نقدی | 1,500,000 تومان |
ثابت
|
خرید |
نام | نوع | واحد | محل بارگیری | نوع پرداخت | قیمت | تغییرات | ||
---|---|---|---|---|---|---|---|---|
سنگ آهن کلوخه صنایع معدنی ایران | سنگ آهن کلوخه | تن | کارخانه | نقدی | 1,347,000 تومان |
ثابت
|
خرید |
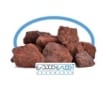
بررسی کاربردها، معضلات و شاخصهای تولید سنگ آهن کلوخه
سنگ آهن کلوخه (Lump Ore) یکی از مهمترین اشکال مصرفی سنگ آهن در صنایع فولادسازی است که بهصورت ذرات درشت (۱۰ الی۳۰ میلیمتر) و با حداقل فرآوری تولید میشود. قیمت سنگ آهن بنابر معادن، روند ساخت، میزان ابعاد، شکل و وزن تعیین شده و در بازار عرضه میشود. این مقاله به بررسی جامع سنگ آهن کلوخه، ویژگیهای فیزیکی و شیمیایی آن، روشهای تولید، مزایا و معایب، و کاربردهای آن در صنعت فولاد میپردازد. همچنین، چالشهای فرآیند تولید و راهکارهای بهبود کیفیت مورد تحلیل قرار گرفته است.
سنگ آهن بهعنوان ماده اولیه اصلی در تولید فولاد، پس از استخراج از معدن نیاز به فرآوری دارد تا به فرمهای قابل استفاده در صنعت تبدیل شود. سنگ آهن کلوخه یکی از این فرمهاست که به دلیل هزینه تولید پایین و سهولت استفاده، سهم قابلتوجهی در تغذیه کورههای ذوب دارد. برخلاف گندله آهن که نیاز به فرآیندهای پیچیدهتری دارد، کلوخه با عملیات سادهتری مانند خردایش و سرند کردن تولید میشود.
تعریف و شاخصههای فیزیکی
این ماده به ذرات درشتی گفته میشود که اندازه آنها معمولاً بین ۱۰ تا ۳۰ میلیمتر است و پس از استخراج، تنها با خردایش و سرند کردن آماده مصرف میشود. به بیان دیگر تولید کلوخه طرحی از آگلومراسیون حرارتی به شمار میآید که اصطلاحاً به آن کلوخهسازی هم میگویند؛ در این فرآیند مواد اولیهی خام در قالب سایزهای کوچکی به کلوخه بدل میشوند. در واقع این روند برای ذوب، تصفیه ذرات کوچک و خاکههای سنگ آهن بدون به وجود آمدن هیج مشکلی باید به شکل این ماده تبدیل شوند.
این محصول از طریق قطعات درشت و متراکم سنگ آهن که در قالب مراحلی متشکل از استخراج و ساخت برآمده از سنگ معادن تولید میشود؛ تودههای این محصول متشکل از درصد فراوانی از آهن که ترکیبات آن حاوی اکسیژن، سلیس، آلومینا و سایر ناخالصیهای طبیعی است. این فرآورده به علت غلظت بالایی که دارد موجب میشود تا نسبت به سنگ آهن خام گزینهی بهتری از نظر اقتصادی در جهت برآورده کردن خوراک کورههای ذوب، بهخصوص در صنعت فولادسازی شناخته شود.
برای خرید سنگ آهن لازم است تا نوع فرآیند تولید آن را در نظر بگیرید؛ قیمت سنگ آهن کلوخه نیز که یک ماده در ذیل سنگ آهن به شمار میرود با توجه به متغیرهای مربوط به ساخت متفاوت است، پس لازم است ویژگیهای آن را در نظر بگیرید تا بدانید کدام شیوه ساخت و کدام قیمت متناسب با مصرف شما به کار میآید. ویژگیهای اصلی و کاربردی این ماده عبارتند از:
- عیار آهن: معمولاً بین ۵۸ درصد تا ۶۴ درصد.
- ناخالصیها: شامل سیلیس (SiO₂)، آلومینا (Al₂O₃) و فسفر (P).
- شکل ذرات: نامنظم و زاویهدار (برخلاف گندله که کروی است).
- تخلخل: کمتر از گندله آهن ولی بیشتر از کنسانتره سنگ آهن.
[caption id="attachment_4410" align="alignnone" width="900"] مقایسه سنگ آهن کلوخه با گندله آهن و کنسانتره سنگ آهن[/caption]
مقایسه با گندله آهن و کنسانتره سنگ آهن
در واقع هر یک از این سنگ آهنها کاربردها و مزایایی بر دیگری دارند؛ به عبارت دیگر روند تولید هر یک از این مواد متفاوت است و بنابر مدل ساختی متفاوتشان کاراییشان در صنعت فولاد وابسته شیوه تولیدشان است. آگاهی از شیوه ساخت موجب میشود تا مصرفکننده بتواند تصمیم بگیرد که کدام از این مادههای اولیه برای او کاربرد بهتری به ارمغان را میآورد. خلاصهی چیستی این سنگ آهنها به شرح ذیل است که تعریف هر یک از مواد را مشخص میسازد:
- گندله: از نرمه سنگ آهن و افزودنیهایی مانند بنتونیت تولید میشود و نیاز به پخت دارد. اندازه آن ۹ الی ۱۶ میلیمتر است.
- کنسانتره: ذرات بسیار ریز (زیر ۱ میلیمتر) با عیار بالا (۶۵ الی ۷۲ درصد) که برای تولید گندله استفاده میشود.
- کلوخه: نیاز به فرآوری کمتری دارد و مستقیماً از سنگ معدن درشتدانه تولید میشود.
مراحل ساخت
برای تولید هرگونه فولاد باید سنگ آهن را از معدن استخراج کرد و مادهی استخراج شده را برای تبدیل به فولاد از مراحل گوناگونی بگذرد. در واقع سنگ آهن را نمیتوان به همان صورتی که از معدن استخراج میشود به کاربرد و باید خرد شوند به کنسانتره سنگ آهن تغیر شکل دهند. مادههای کلوخه و گندله سنگ آهن جزو دستههایی هستند که باید طی فرآیند بدل به محصولی کابردش شوند تا بهعنوان مادهی اولیه در کارخانههای مورد استفاده قرار گیرند. باتوجه به این نکته مراحل شکلگیری سنگ آهن کلوخه به شرح مراحل زیر است:
۱. استخراج از معدن
سنگ آهن خام با عیار حدود ۵۰% از معادن روباز یا زیرزمینی استخراج میشود. روشهای متداول استخراج شامل حفاری، آتشباری و بارگیری است.
۲. خردایش اولیه و ثانویه
- سنگشکن فکی یا ژیراتوری: کاهش ابعاد تا ۲۰۰ الی۱۵۰ میلیمتر.
- سنگشکن مخروطی: کاهش بیشتر تا ۵۰ الی۳۰ میلیمتر.
۳. غربالگری و دانهبندی
ذرات خردشده توسط سرندهای ارتعاشی به سه دسته تقسیم میشوند:
- ذرات ریز: زیر ۱۰ میلیمتر برای فرآوری بیشتر یا دورریز.
- ذرات کلوخه: ۱۰ الی ۳۰ میلی متر برای محصول نهایی.
- ذرات درشت: بالای ۳۰ میلیمتر برای بازگشت به سنگ شکن.
۴. شستشو و جدایش ناخالصیها
برای افزایش عیار آهن، از روشهای زیر استفاده میشود:
- شستشو با آب: حذف مواد ریز و ناخالصیهای سطحی.
- جداکنندههای مغناطیسی: جدایش کانیهای آهندار از گانگ (مواد بیارزش).
۵. خشککردن و انبارش
رطوبت سنگ آهن کلوخه باید به زیر ۵ درصد کاهش یابد. سپس در سیلوها یا انبارهای سرپوشیده ذخیره میشود.
[caption id="attachment_4411" align="alignnone" width="900"] اهمیت و کارکرد سنگ آهن کلوخه[/caption]
اهمیت و کارکردها
۱. استفاده در کوره بلند
- به عنوان بخشی از بار کوره همراه با کک و سنگ آهک.
- ایجاد تخلخل مناسب برای بهبود احیای آهن.
۲. استفاده در احیای مستقیم
- در برخی روشها مانند میدرکس (MIDREX) برای تولید آهن اسفنجی.
۳. مصارف دیگر
- تولید سیمان (به عنوان ماده اصلاحکننده).
- مصارف ساختمانی در موارد خاص.
مزایا و معایب در صنعت فولادسازی
این ماده همانطور که گفته مانند سایر سنگ آهنهای دیگر از مزیت و مشکلاتی برخوردار است. مهمترین مزیتهای این محصول عبارتند از:
- هزینه فرآوری پایین: نیاز به فرآیندهای پیچیده مانند گندلهسازی ندارد.
- کاهش مصرف انرژی: در مقایسه با تولید کنسانتره و گندله.
- قابلیت استفاده مستقیم: در کوره بلند بدون نیاز به تبدیل.
مهمترین معایب این فرآورده عبارتند از:
- عیار پایینتر نسبت به کنسانتره و گندله که بر کیفت نهایی هر محصول تأثیر میگذارد.
- حساسیت به خردشدگی در حملونقل و انبارداری؛ که میتواند موجب هزینهای اضافی برای مصرفکننده شود.
- توزیع نامنظم اندازه ذرات ممکن است عملکرد کوره را تحت تأثیر قرار دهد.
چالشها و پیشنهاداتی برای رفع مشکلات
این سنگ آهن از معضلاتی برخوردار است که سبب میشود تا کیفیت آن به هنگام تولید پایین آید و اگر کیفیت کاسته شود این امکان را به وجود تا بهعنوان مادهی اولیه بر محصولهای فولادی اثرات منفی بگذارد. در تحقیقات صورت گرفته توسط محیطهای پژوهشی اعماز دانشگاه و انجمن صنعت و معدن میتوان چالش به شرح ذیل صورتبندی کرد:
- کاهش ذخایر سنگ آهن با عیار بالا.
- افزایش نیاز به پر عیارسازی برای حذف ناخالصیها.
به همین منظور پیشنهادی که از سوی مراکز پژوهشی برای حل این چالشهای مطرح شد بهصورت کلی به شرح ذیل است:
- استفاده از روشهای ترکیبی: مانند سرند کردن و هیدروسیکلون برای دانهبندی دقیقتر.
- بهبود جدایش مغناطیسی: برای افزایش عیار آهن.
- ترکیب با گندله: برای بهبود عملکرد کوره بلند.
سهمی پایین در تولید اما مقرونبهصرفه!
این ماده بهعنوان یکی از مقرونبهصرفهترین اشکال سنگ آهن، نقش حیاتی در صنعت فولاد ایفا میکند. اگرچه به دلیل عیار پایین، سهم آن در مقایسه با گندله در حال کاهش است، ولی هنوز در بسیاری از کورههای بلند جهان مورد استفاده قرار میگیرد. توسعه فناوریهای جدید در پر عیارسازی و بهینهسازی فرآیند تولید میتواند موقعیت این محصول را در زنجیره تأمین فولاد تقویت کند.